Posts Tagged ‘Manufacturing’
MumbaiPav.com – Manufacturing of Camera Lenses

Raw Materials Coating, Barrel, Housing for the camera lens, Lens mounts The Manufacturing Process Grinding and polishing lens elements 1 Optical glass is supplied to lens manufacturers by specialized vendors. Usually, it is provided as a “pressed plate” or sliced glass plate from which the elements are cut. The glass elements are shaped to concave or convex forms by a curve generator machine that is a first-step grinder. To reach the specifications for its shape, a lens goes through a sequence of processes in which it is ground by polishing particles in water. The polishing particles become smaller in each step as the lens is refined. Curve generation and subsequent grinding vary in speed depending on the frailty, softness, and oxidation properties of the optical materials. After grinding and polishing, the elements are centered so that the outer edge of the lens is perfect in circumference relative to the centerline or optical axis of the lens. Lenses made of plastic or bonded glass and resin are produced by the same processes. Bonded materials are used to make lenses with non-spherical surfaces, and these lenses are called “hybrid aspherics.” The aspherical surfaces of these lenses are completed during centering. Coating lenses 2 Formed lenses are coated to protect the material from oxidation, to prevent reflections, and to meet requirements for “designed spectrum transmission” or color balance and rendition. The lens surfaces are carefully cleaned before coating …
Video Rating: 4 / 5
C & M Corporation Manufacturing in Mexico
www.offshoregroup.com Welcome to C & M Corporation’s Mexico cable assemblies manufacturing facility. C& M Corporation’s manufacturing in Mexico plant is located in Empalme, which is located in the south of the border state of Sonora in The Offshore Group’s Bella Vista industrial park. The facility is strategically located with access to the main state highway, and is less than 250 miles away from the US / Mexico border, Nogales Arizona. It features 18650 square feet which include: a warehouse, shipping and receiving docks and a continuously improved production floor. This manufacturing facility also features several lean cells, which cover more than 65 percent of the total production output. Each one of them has a highly motivated high performance team, with knowledge of lean manufacturing principles, to achieve one-piece flow, guided by a support team member that trains, helps and make things happen. This allows for low-volume and high-mix manufacture of cable assemblies, custom wire and cable and coil cords. C & M Mexico facility has a segregated production area, ideal for medical device manufacturing in Mexico, which requires special handling conditions. Injection molding services include top-notch equipment, aided by C & M tooling design capabilities to deliver high quality injection molding solutions. Custom cable assemblies manufacturing services are provided through coil cords capabilities. C & M Mexico performs complete electrical and mechanical First Article …
Video Rating: 5 / 5
Fraction Contraption Plastic Manufacturing
Learn how the plastic injection molding process works with the Fraction Contraption
Video Rating: 5 / 5
This is not your typical floor liner! Existing floor liners in the market today are constructed of extruded plastic materials vacuum formed to fit the vehicle. Rugged Ridge has taken a completely different approach to floor protection. Each All Terrain Floor Liner is injection molded for superior fit and quality. The injection molded process, though more expensive to develop, allows us to create a floor liner that has exacting measurements for better fit and finish along with a deeply formed perimeter wall for maximum coverage. Each All Terrain Floor Liner has chevrons that are up to 3/8″ deep. That is up to 3 times the depth of other floor liners! We call this true “Deep Tread Technology”!
Video Rating: 0 / 5
Engine Cover Manufacturing and Assembly Process.mpg
This video shows a typical molded engine cover being robotically removed from the injection molding tool which was opened in the press after completing the molding cycle. The robot takes the cover to the operator who places the cover into the hot stamp decorating station. The embossed letters and numbers are decorated with a silver hot stamped film. The decorated cover and other components are then loaded into a fully error proofed assembly fixture. After approved assembly, the operator is allowed to load the finished part into the shipping container. The approval to pack is shown by a green light at the top of the box.
Video Rating: 0 / 5
Daher Foam Products Manufacturing Process Step 2: De-molding & Cleaning
This video contains a brief overview of the Daher Manufacturing Inc. de-molding and cleaning process. Once the injected foam has cured, the mold is pried open and pressured air is used to remove the foam product. Each mold is carefully coated prior to injection, ensuring a flawless finish. Some of the product’s excess material is removed before it is passed to the trimming department. The mold is thoroughly cleaned in preparation for future use. Visit us at www.daherproducts.com for more information or call toll-free 1-888-503-2437.
Video Rating: 0 / 5
Plastic Injection Molding – Overview from ALTEK Manufacturing
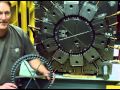
Learn more about plastic injection molds and plastic injection molding in this brief video from ALTEK Manufacturing. Every plastic injection mold project includes a rigorous review process, including part and mold design reviews, mold testing, and first article inspection.
Maetta www.maetta.ca
The SelectConnect Laser Direct Structuring (LDS) process for manufacturing 3D-MID
An overview of the SelectConnect process of making three dimensional molded interconnects (3D-MID) using the LPKF Laser Direct Structuring (LDS) method of integrating electrical circuits onto injection molded housings and components.
Video Rating: 5 / 5

This module discusses the fundamentals of part cooling; one of the major aspects of the injection molding process. It also features a short instructive excerpt from one of the A. Routsis Associates courses intended to jump start your training initiative.
Injection Molding vs. Direct Digital Manufacturing
Learn about injection molding versus direct digital manufacturing in this presentation. Low-volume manufacturing can mean producing anything from 1 part to 5000 parts. In some cases, it’s possible to reduce low-volume production costs by 75% or more, by replacing traditional tooling with direct digital manufacturing (DDM). But DDM isn’t for every application. Determine if this alternative process is right for your company by watching this presentation. Video re-posted with permission from Stratasys.
Video Rating: 5 / 5
Daher Foam Products Manufacturing Process Step 1: Foam Injection.m4v
This video contains a brief overview of the Daher Manufacturing Inc. foam injection process. The mold consists of two separate pieces which are tightly secured together. Using the Reaction Injection Molding (RIM) process, the foam is forced into the mold where it expands and conforms to the shape of the mold. The RIM process allows a variety of materials to produce an almost infinite possibility of shapes and densities designed to meet our customer’s specific needs. Visit us at www.daherproducts.com for more information or call toll-free 1-888-503-2437.
Q&A: manufacturing process of acrylic guitar? ?
Question by Nick S: manufacturing process of acrylic guitar? ?
Hi, I’m currently doing a piece design technology work in which i have to outline the main process in making an acrylic guitar base. However i am unable to find any information which is clear and easy to understand, basically can anyone tell me how it would be done? eg. blow molding or injection molding.
Thanks.
Best answer:
Answer by RWhycome
I’m not sure it’s the most practical method for making an acrylic guitar body but here’s one way to do it that wouldn’t require an expensive mold. You would start with a slab of acrylic ordered in the desired thickness of the body. The profile of the body would then be rough cut slightly oversize on the band saw. Next the profile and the internal cavities would be cut to shape by a template guided router or a CNC milling machine. Finally the machined edges would need to be sanded smooth and polished either mechanically and or chemically until the edges become clear. To find out for sure how it’s done you should contact Ampeg, a company best known for it’s guitar amplifiers. Back in the sixties Ampeg, in collaboration with a guy named Dan Armstrong produced a guitar and a bass that had bodies made out of Plexiglass. If anyone knows how it’s done these guys do. Best of all the company is still in business and has recently reissued these plexiglass guitars. Give them a call. Hopefully they will help you out. Good luck.
Give your answer to this question below!