Posts Tagged ‘Parts’
CATIA V6 | Mechanical Engineering | Bend Part Design | Folded parts from sheetmetal to paper boxes
Expands into manufacturing preparation CATIA V6 strengthens the manufacturing preparation process with Bend Part Design, which enables users to quickly create folded parts across multiple disciplines from sheetmetal to paper boxes. CATIA V6R2011 enriches its mold tooling solution with CATIA Mold Tooling Design product. This specialized application covers the complete tooling process for mold tooling injection designers.
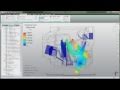
Want more information after viewing this video? Be sure to visit www.autodesk.com and www.SIMSquad.com. Autodesk® Simulation software, part of the Autodesk® solution for Digital Prototyping, provides a range of mechanical simulation tools to help designers, engineers, and analysts make decisions earlier in the engineering design process. With these tools, you can predict the real‐world performance of your product, helping to save the time and money required to build multiple physical prototypes. Autodesk® Simulation software lets you start with mainstream tools and then expand your toolkit to include more advanced simulation such as mechanical event simulation, computational fluid dynamics (CFD), and multiphysics—without the need to learn new workflows. Real-world product behavior is often the result of multiple physical effects interacting simultaneously. With Autodesk® Simulation Multiphysics software, you can study these effects by combining results from different analysis types to help predict a product’s real-world performance. The setup of multiphysics simulations is made easier through the use of standard engineering terminology, workflow guidance, and user-friendly tools and wizards that automate the transfer of simulation results between multiple analyses—letting you focus on product performance, not advanced numerical or simulation methods. Autodesk® Simulation software includes modeling flexibility for multiphysics simulations, allowing you to create meshes …
DIY Plastic Parts

I’ve got one word for you. “Plastics” Yes, it’s what whales and seals are having for lunch.
Video Rating: 4 / 5
There is an updated video of this, now WITH AUDIO!!! Here is a quick fly through of how to make a plastic injection mold by using Solidworks. First you can see that I am making a simple solid, make sure that it has ample draft. The radii are un important but aids in presentation. Second I am shelling the object to a suitable thickness, remember with plastics a consistent wall thickness is key! I then make a sketch that will define the limits of the mold itself. Next I am defining the parting line, this is the line that Solidworks uses to define the separation of the mold cavity and core sides. I am also turning on draft analysis to help show me that my object is of suitable geometry to part. After that, you cant see it, but I check for shut-off surfaces; I have none. Then by selecting the parting lines I can then create a parting surface, this is the surface that the mold cavity will shut off against when closed. Once those steps are completed I can define my tooling slip, I choose interlock and the approximate thicknesses of each mold half. From there I move each half apart to reveal a mold! When all the steps have been done save the cavity and core sides into seperate files. Next CORES, SLIDES, AND LIFTERS!
Video Rating: 1 / 5
Aligned Parts Assembly System
APAS Automation captures part alignment upon creation and maintains it throughout subsequent processes up to final assembly.
Video Rating: 4 / 5
Injection of precision plastic parts
The movie shows the injection process to manufacture high quality plastic parts, mostly for the automobile industry, using advanced automation including robotic arms. This movie is part of a series of nine videos (“Industrias”) designed to assist courses in industrial operations and engineering, and produced during 1998/9 by AESBUC ETGI with financial assistance of PEDIP2 program. Recorded in the new factory of IberoOleff, Pombal (Leiria).
Video Rating: 0 / 5
Custom Molded Plastic Parts – From Design to Delivery!

www.CustomMoldedPlasticParts.com Custom Molded Plastic Parts will provide a step by step process from design to final production, develop quicker to market approaches in the design stage, offer advice on manufacturability of the product & much more…
Video Rating: 0 / 5
CSIT Trading Co., Ltd Established in 2009, we are specialized in Injection molding,Die casting,CNC process,Puncher process,Electric painting,Powder coating. We are equipped with a modern fleet of machineries and provide the highest standard quality products.
Video Rating: 5 / 5
How to make carbon fiber parts
How to make carbon fiber parts
Video Rating: 4 / 5
Just in! New for June 2010! The Kryptonite line of ultra strong, virtually UNBREAKABLE Flair Bottles. This new line of flair bottles uses an injection molding process rather than blow molding therefore guaranteeing a PERFECTLY FORMED flair bottle every time. Perfectly balanced. Perfectly weighted. Perfectly solid. And a perfect feel and grip. These Kryptonite bottles are as tough as they get, and are made from our trade secret “Kryptonite” material! Choose from several different styles. We offer the traditional solid white 750 ml bottle, as well as clear and colored transparent bottles. And to bring a little more flair to the show we are offering this bottle in a brilliant neon green (glows under a black light) … a powerful kryptonite effect! Lighted Flair Bottle is Below. Priced right! Stay tuned for deocated ones.
Q&A: What factory processes to make guitar parts?
Question by cajunwarrior: What factory processes to make guitar parts?
I was wondering for factory-made guitars, what processes are used to mass produce guitar parts. As the Tone controls are most likely a thermoplastic and so made by injection moulding, but how about the other parts of a guitar? Like the scratchplate?
Best answer:
Answer by dreamchanter
See how Gibson guitars are made:
http://dsc.discovery.com/videos/some-assembly-required-gibson-guitars.html
or
http://science.discovery.com/search/results.html?query=guitar&search.x=31&search.y=9&search=search
Add your own answer in the comments!
Q&A: Can I manufacture phone parts of existing phones?
Question by Kyrie Eleison: Can I manufacture phone parts of existing phones?
Hello guys. With all these phone parts that can get dinged and scraped, I was wondering if it is possible to manufacture phone parts or any other parts of common consumer electronics eg. blackberry, nokia, htc… (such as battery covers, face plates). I’m sure I cannot put their branding on it (like blackberry’s or any other company) but just sell them as generic parts. Is this possible?
Oh, and if it makes any difference. If I would do it, the plastic parts would be injection molded and cranked out of the machine just like that.
Best answer:
Answer by Phil
You would really need an attorney to be sure. If you aren’t branding them, then the only obstacle would be if there was actually a patent on the case or its parts. That’s pretty unlikely, but you really would need to be sure.
What do you think? Answer below!
8 Ways to Design Injection Moulding Parts with Consideration for Process
8 Ways to Design Injection Moulding Parts with Consideration for Process
To ensure a successful finished product, you need to be aware of the process that goes into making your component. This should be at the forefront of your mind when considering the design of your part. Injection moulding will provide you with the component you want, and if you are able to consider its process in your design concepts you can guarantee a successful finished product.
Coherence. Try to make your design uniform throughout. That is, wall thickness, rib thickness and corner radii, for instance, should all be the same values. This will help the part to cool uniformly.
Wall thickness. Keeping your walls thin will ensure a faster cooling rate and less materials used. Lower cooling rate and less materials used will result in a shorter cycle time, allowing you more parts in a shorter amount of time, for less production cost.
To strengthen parts, ribs are more effective than thicker walls. Adding ribs at right angles to a wall will add considerably to its overall strength. It is a common mistake to thicken the walls of a design to achieve this effect when ribs are a cheaper and more effective option.
Ribs should be about half the main wall thickness.There can be some leniency here, but not too much or the ribs will be completely ineffective. Half is the generally accepted standard and is more than enough to increase a wall’s strength.
Corners and edges should be rounded wherever possible. Sharp edges do not always come out perfectly when the part is ejected from the mould.
Add a slight angle to the sides of your mold to allow easy release. A one or two degree angle should be applied to the mould on the face perpendicular to the parting line. This will allow for easy removal of the part from the mould.
Avoid undercuts. Protrusions on the part that will snag on the mould core or cavity when it is opened can make it impossible to remove from the mould.
Where possible, use lighter colours for your moulds. The mould is already cool when the molten material is being injected. As such it begins the setting process immediately and will sometime leave setting patterns. Using lighter colours will help y.to hide these patterns.
Injection moulding is the industry standard for creating lasting, quality parts. To be able to take advantage of this technology your design must meet its minimum requirements. Small considerations are all it takes and the result is a successful product that will meet all of your quality needs.
Dienamics is the only company in Brisbane to offer the complete service of Industrial Design, Toolmaking and Manufacturing. We specialise in the custom moulding of components using engineering thermoplastic resins. For more information, visit Injection Moulding
.
Algor Simulation 2011 and Moldflow — Simulation of Plastic Parts
Autodesk Algor Simulation users designing plastic parts can now access the extensive Autodesk Moldflow material database, containing grade-specific material properties for more than 8000 thermoplastic resins. For products that use a fiber-filled material, export your Autodesk Algor Simulation model to Autodesk Moldflow software in order to simulate the plastic injection molding process and help predict the orientation of fibers in the manufactured part. With the combination of Autodesk Algor Simulation and Autodesk Moldflow software, you can better predict the real-life behavior of your plastic parts. Learn more about Autodesk Algor Simulation 2011: www.autodesk.com
Video Rating: 5 / 5